Innovazione di prodotto e di processo con un occhio sempre attento alla sostenibilità ambientale. Questa la filosofia di Project for Building, azienda di Mornico al Serio (Bergamo) specializzata nella produzione di prodotti in plastica riciclata che contribuiscono all’innovazione dei sistemi tradizionali dell’edilizia. Ne parliamo con il Ceo Giancarlo Zanini.
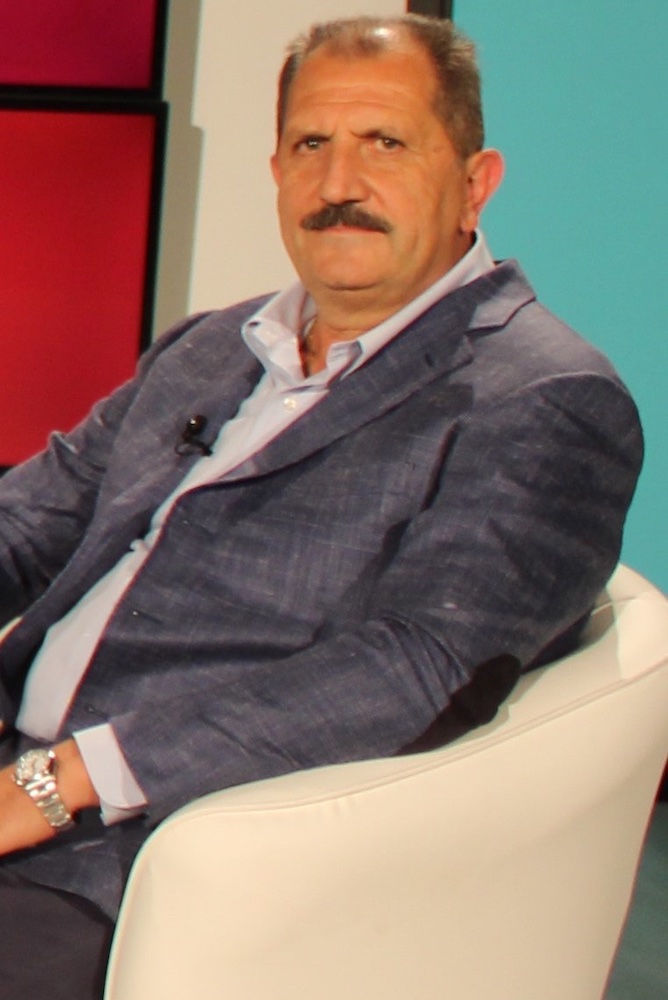
Domanda. Project For Building nasce nel 1995 con l’obiettivo di produrre casseri per edilizia in plastica riciclata. Qual è la sua storia?
Risposta. L’azienda inizialmente aveva un unico prodotto, il Granchio, un cassero a perdere in plastica riciclata per le fondazioni destinato alla realizzazione di vespai con altezza 40 centimetri. L’obiettivo era bloccare la fuoriuscita di gas radon e la risalita di umidità dal terreno, in accordo con la raccomandazione della Commissione Europea del 21 febbraio 1990. In Italia non esistevano ancora prodotti di questo tipo, quindi la nostra soluzione è stata brevettata decretando la nascita dell’azienda. All’inizio non avevamo macchine per lo stampaggio, quindi la produzione era esternalizzata. Dal 1995 in poi lo sviluppo è stato molto rapido, tanto che sono nati altri stampi ed è stato perfezionato il design del prodotto, inserendo nuove altezze.
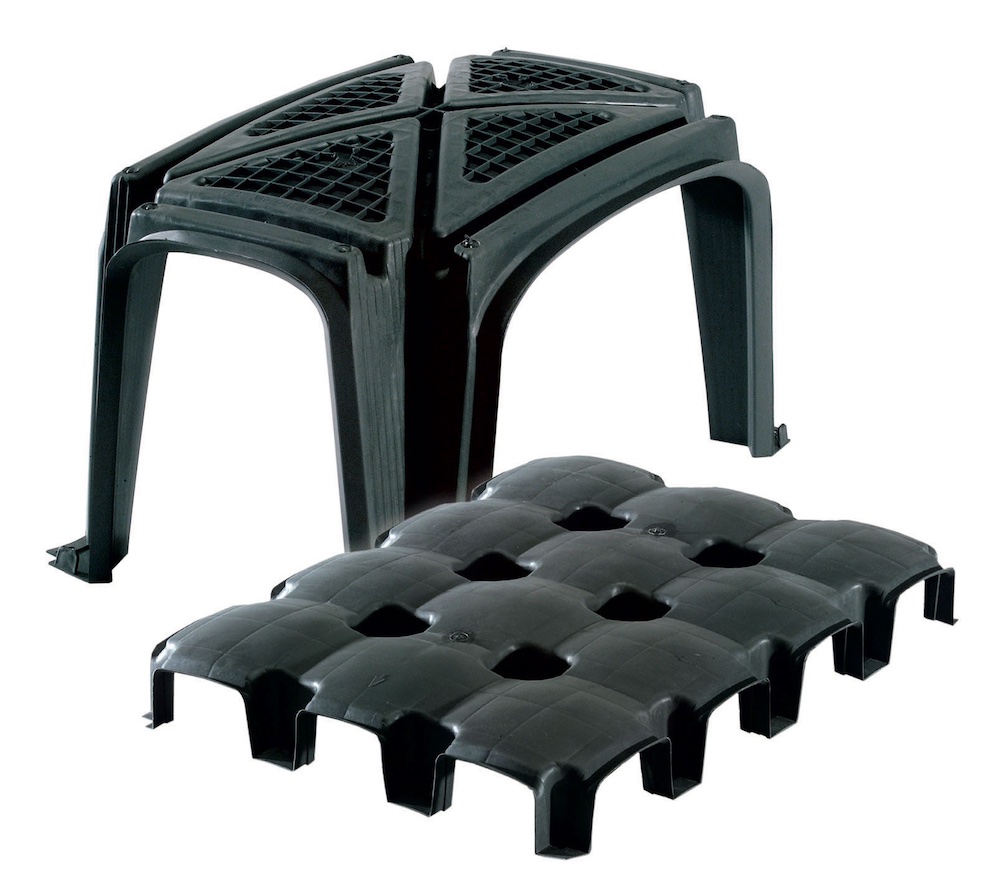
D. Quali sono stati i passi successivi?
R. Partendo dal Granchio sono stati creati nuovi prodotti in diverse altezze: oggi partiamo da 5 centimetri per arrivare a 130 centimetri. Nel frattempo, è stato ottimizzato il design del prodotto, soprattutto per le altezze più elevate, incorporando alla base delle gambe, in modo da assicurare maggiore stabilità e velocità in fase di posa. Consolidando la produzione di questo elemento, ne sono sorti altri sempre in plastica riciclata e legati al mondo dell’edilizia. Oltre alla linea Granchio, Hercules e Mini Hercules, specifici per le fondazioni, sono nati nuovi elementi per il garden, come Skudo, adatto alla protezione dell’impermeabilizzazione dei muri contro terra. Abbiamo poi progettato Drain Floor, elemento per la realizzazione dei giardini pensili che consente di proteggere la superficie del terrazzo e garantire al contempo l’alimentazione idrica per lo sviluppo vegetativo. Un altro elemento che ricopre un’importante fetta del nostro mercato è Green Parking, per la realizzazione di parcheggi e percorsi carrabili inerbati. Parallelamente allo sviluppo di nuovi prodotti, l’azienda ha sempre avuto una forte attenzione alla sostenibilità, puntando sull’utilizzo di materiali di seconda vita. Nel 2000 abbiamo deciso di internalizzare la produzione acquistando una decina di macchine per lo stampaggio, e nel 2009 ci siamo trasferiti nell’attuale sede dove abbiamo dato vita anche a una innovativa linea di riciclo.
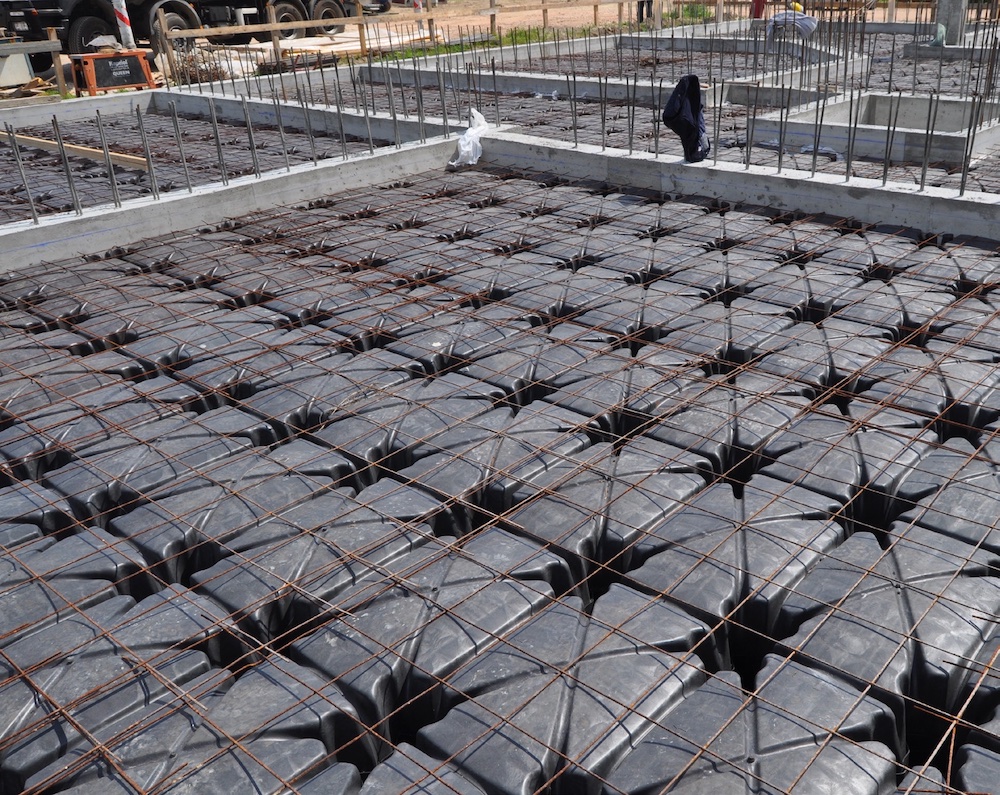
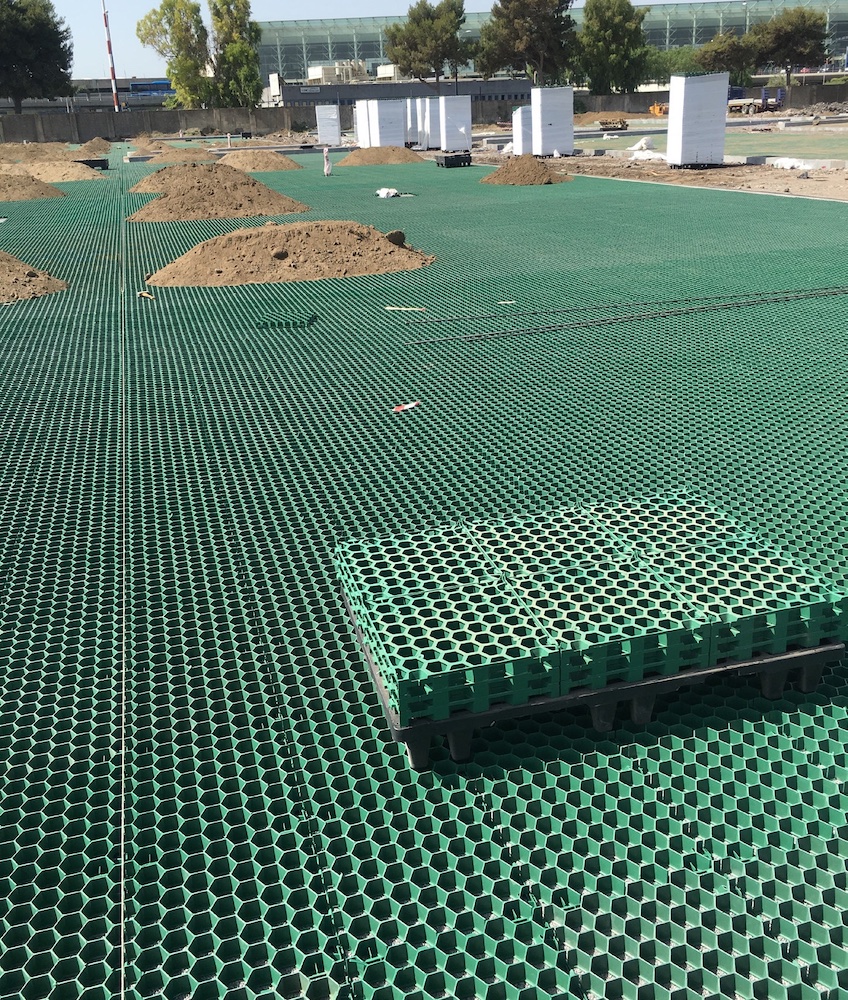
D. Come funziona il processo del riciclo?
R. Ritiriamo i rifiuti in polietilene e polipropilene e li utilizziamo direttamente per la produzione dei nostri prodotti, in un processo di economia circolare. In Europa ci sono pochissime realtà che partono dal rifiuto e arrivano al prodotto finito. Ogni giorno in stabilimento arrivano circa 40 tonnellate di rifiuti: negli anni abbiamo selezionato accuratamente i fornitori, quindi la plastica che arriva dalle discariche e dai centri di lavorazione o smistamento è già imballata e pronta per essere lavorata. Abbiamo due linee di lavorazione: una per le plastiche rigide, che vengono macinate, e una per quelle morbide, che vengono tranciate e finiscono poi in un densificatore. Alla fine, facciamo una miscela fra plastiche morbide e rigide che vengono incanalate nella trafila, fino ad arrivare alla produzione del granulo, poi immesso direttamente nel reparto per lo stampaggio. Per quanto riguarda i pneumatici dismessi, utilizzati per i prodotti dedicati all’isolamento acustico, invece, arrivano già macinati e da lì realizziamo la miscela per la produzione dei pannelli.
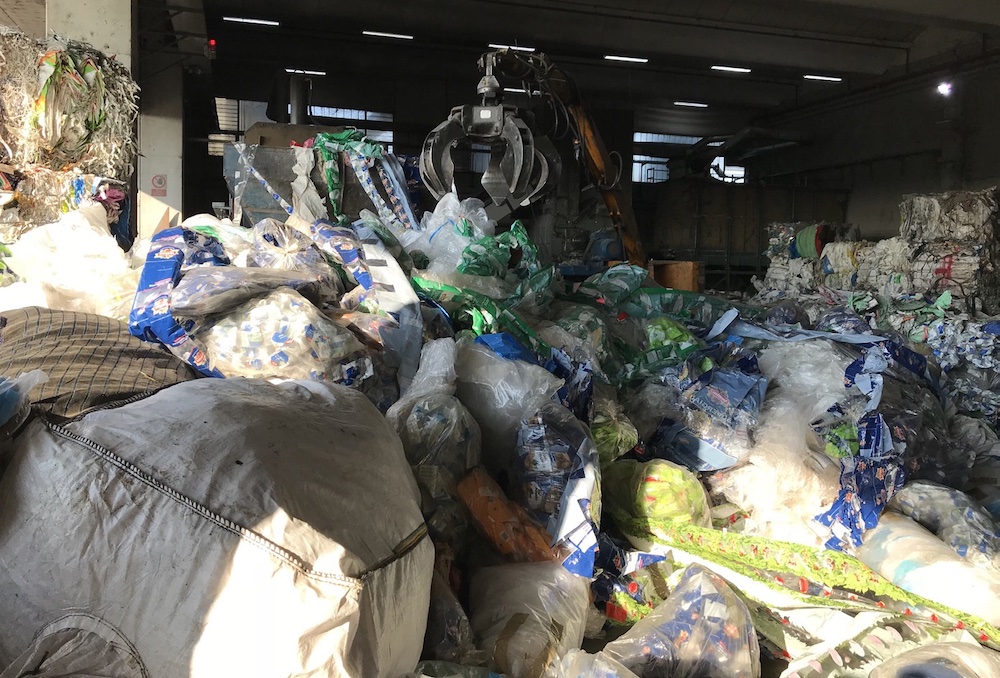
D. Come è organizzata ora l’azienda?
R. Tutta la produzione è concentrata nella sede di Mornico al Serio (Bergamo). Attualmente l’impianto ospita 20 macchine per lo stampaggio plastico. Abbiamo anche macchinari molto esclusivi, che utilizziamo per lo stampaggio conto terzi, come una innovativa pressa a iniezione classica da 5 mila tonnellate. Attualmente siamo in una fase di ampliamento: verso i primi di luglio abbiamo montato una nuova campata di capannone e nei primi mesi del 2024 inseriremo altre cinque presse, arrivando a 25 macchine, che ci consentiranno di allargare l’offerta per il settore edile. L’idea è anche quella di ampliare anche la parte del riciclo, inserendo una nuova trafila proprio per incrementare i quantitativi di materiale riciclato che produciamo, con l’obiettivo di ridurre sempre di più il materiale di scarto.
D. Com’è articolato oggi il vostro catalogo?
R. Oltre all’edilizia e al garden, nel 2007-2008 abbiamo dato vita a una linea di prodotti per l’isolamento acustico, sempre basati sull’utilizzo di materiale rigenerato. In particolar modo, per i prodotti acustici utilizziamo granuli di gomma ottenuti dal recupero degli pneumatici dismessi. Grazie a una miscela ottimale, che riesce a fare da collante con questa gomma, abbiamo dato vita a questa gamma di prodotti per il benessere acustico.
D. Come si compone la vostra offerta per il settore dell’isolamento acustico?
R. Abbiamo prodotti per l’isolamento orizzontale e verticale, oltre a una linea di antivibranti. Per isolamento orizzontale intendiamo i materassini sottomassetto e sottopavimento, mentre per l’isolamento verticale abbiamo delle lastre di cartongesso accoppiati con pannelli in gomma, destinate sia per le pareti a secco che per le pareti in contro placcaggio. La nostra gomma, essendo estrusa, riesce a dare una finitura particolare al pannello. In particolare, l’originale geometria rigata su una faccia del pannello consente un isolamento acustico dai rumori aerei di classe superiore. La nostra sfida per i prossimi anni sarà appunto quella di creare soluzioni antivibranti ad hoc per il settore ferroviario. Ci stiamo già lavorando e abbiamo realizzato test specifici molto incoraggianti.
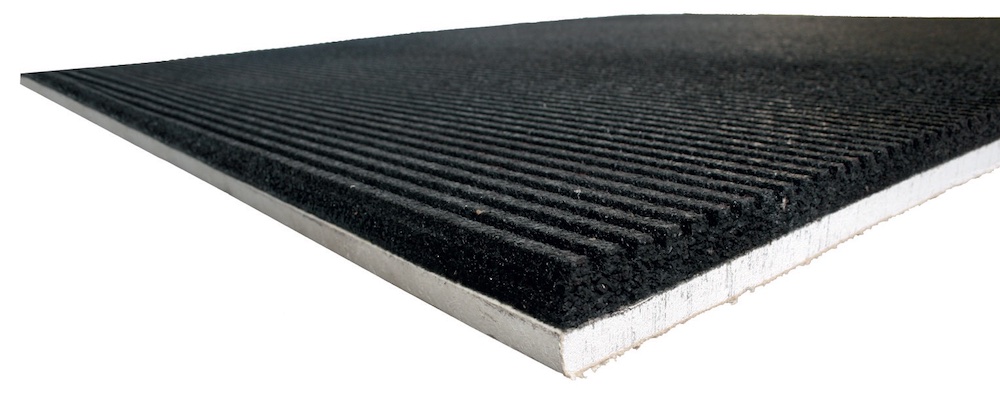
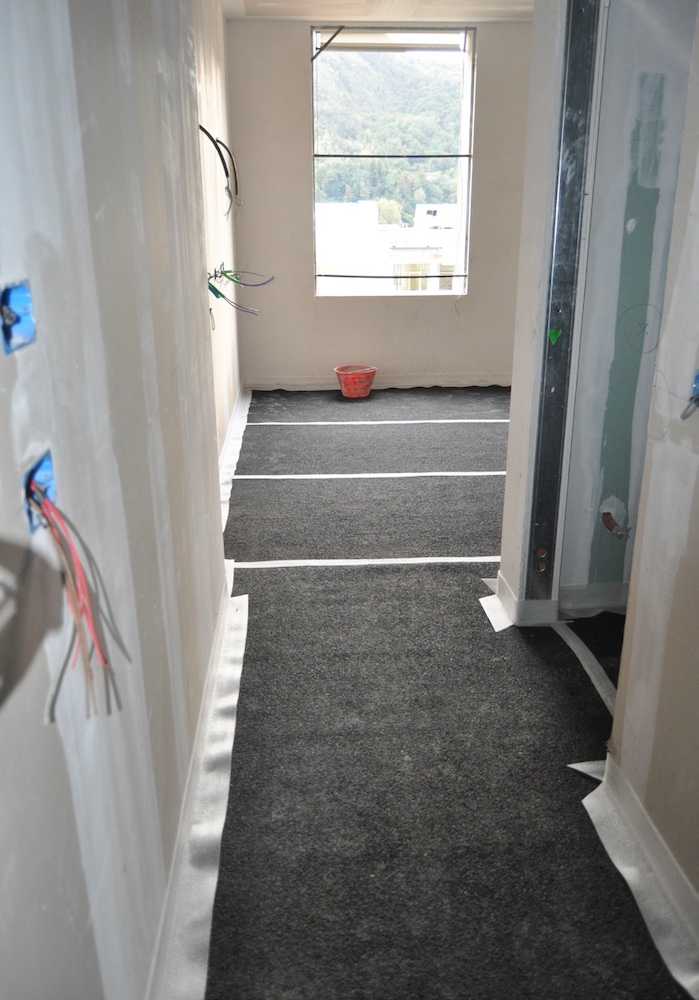
D. Torniamo al settore dell’edilizia. Oltre al Granchio, quali sono le caratteristiche dei prodotti della linea Hercules?
R. La linea Hercules è nata come risposta all’esigenza di creare un vespaio più alto. Ovviamente creare un unico elemento che raggiungesse un’altezza fino a 130 centimetri era impossibile, quindi abbiamo deciso di creare una base a cui andare a giuntare quattro gambe. In questo modo l’operatore può essere sicuro di camminare sopra un elemento sicuro e resistente, ma soprattutto questa soluzione consente di portare a termine il getto di calcestruzzo in un’unica fase, velocizzando le operazioni in cantiere.
D. I casseri sono solo per le fondazioni o anche per i solai?
R. Abbiamo anche prodotti destinati ai solai. La linea destinata a questo tipo di applicazione si chiama Rapido ed è un elemento utilizzato per le realizzazioni dei solai con i travetti ad armatura lenta. È un’alternativa alle pignatte tradizionali in laterizio. Questo elemento in plastica viene controsoffittato e consente di non gravare sulla struttura esistente grazie al suo peso ridotto.
D. I vostri prodotti richiedono particolari competenze per la posa?
R. Assolutamente no. Sono prodotti molto semplici e intuitivi. Per la linea Hercules abbiamo realizzato un video tutorial per mostrare come base e gambe vanno assemblate, ma la posa è veramente molto semplice. Gli altri prodotti hanno sistemi veramente facili di aggancio che sono stati studiati proprio per ottimizzare i tempi di realizzazione in cantiere.
D. Quali sono le differenze rispetto agli altri prodotti presenti sul mercato?
R. Innanzitutto, il nostro plus più importante è che i prodotti sono realizzati al 100% in plastica riciclata e certificati Plastica Seconda Vita. Inoltre, abbiamo un controllo completo della filiera: siamo molto attenti alla qualità dei prodotti e, grazie al centro di riciclo interno, siamo in grado di curare ogni aspetto fino al prodotto finito. Un altro vantaggio con l’utilizzo dei nostri prodotti è il minor utilizzo di calcestruzzo al metro quadro grazie alla particolare geometria dei nostri elementi, soprattutto nelle altezze più elevate da 65 centimetri in su. La facilità di posa e la sicurezza sono altre due caratteristiche molto importanti, oltre al fatto di consentire un getto unico, anche nelle altezze più elevate. Il sistema di incastro tra base e gambe che abbiamo progettato per la linea Hercules è molto robusto e consente di dare stabilità all’elemento e agevolare la posa, in tutta sicurezza e ottimizzando tempo e materiale.
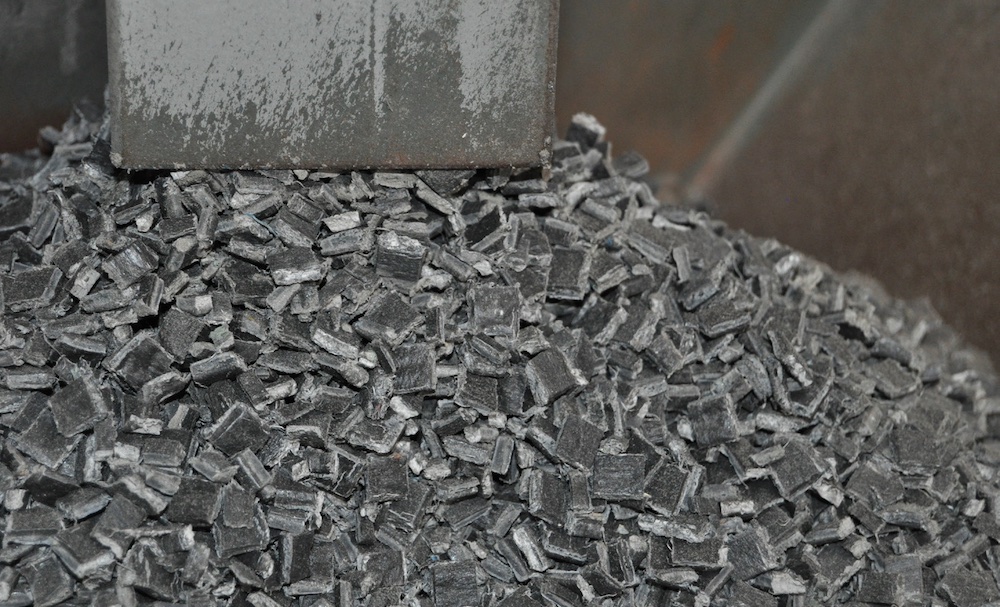
D. Qual è il prodotto più richiesto?
R. Parlando in quantitativi nei primi sei mesi del 2023 abbiamo venduto 540 mila metri quadri tra Granchio e i prodotti della linea Hercules.
D. Siete distribuiti in tutta Italia?
R. Sì. Teniamo molto al servizio e per noi è fondamentale che i nostri prodotti siano immediatamente disponibili. Riusciamo a spedire nell’arco delle 24-48 ore e questo aspetto è molto apprezzato. In più abbiamo, lungo tutto il territorio nazionale, un centinaio di depositi in cui i nostri clienti possono trovare quasi tutta la nostra gamma di prodotti in stock. Molto spesso le stesse rivendite edili che distribuiscono i nostri prodotti fanno da deposito.
D. La vostra offerta è piuttosto ampia: come vi presentate ai progettisti?
R. Quello dei progettisti è un nuovo canale su cui stiamo investendo. A novembre alla fiera Made Expo di Milano lanceremo un nuovo prodotto molto tecnico che sarà dedicato proprio al mondo dei progettisti. In vista di questa novità abbiamo già ampliato il nostro organico interno con un nuovo ingegnere che farà da tramite fra l’azienda e i professionisti e abbiamo anche sviluppato un software di calcolo dedicato a questo nuovo prodotto che sarà dato in dotazione ai progettisti.
D. Considerate sufficiente la competenza di distributori e installatori?
R. Per quanto riguarda i nostri attuali prodotti assolutamente sì. Per i nuovi progetti che abbiamo in serbo per il futuro probabilmente dovremmo investire in formazione.
D. C’è una maggiore sensibilità verso il problema della sostenibilità?
R. Negli ultimi anni notiamo una maggiore sensibilità, un po’ dovuta ai vari obblighi normativi come i Cam, un po’ per un effettivo cambiamento culturale. Diciamo che questa sensibilità si avverte più a livello di chi progetta, che non nelle imprese.
D. Oltre all’impianto di riciclo, come l’azienda mostra la sua forte sensibilità per l’ambiente?
R. Abbiamo da poco installato pannelli fotovoltaici su tutta la superficie del capannone e abbiamo installato un cogeneratore a gas. Tutto quello che viene consumato viene trasformato in energia, quindi non ci sono dispersioni di nessun tipo. Puntiamo inoltre a implementare l’impianto di rigenerazione della plastica nel prossimo triennio.
D. Come vi ponete nei confronti della progettazione Bim?
R. Già da anni la nostra azienda mette a disposizione dei progettisti una libreria Bim della maggior parte dei prodotti. Nata come una sfida, questa iniziativa sta avendo molto riscontro, anzi negli ultimi anni abbiamo notato un incremento dei download dei file Bim. È un metodo che prenderà sempre più piede nei prossimi anni, anche per una questione di certificazioni. Entro fine anno puntiamo a completare la nostra libreria.
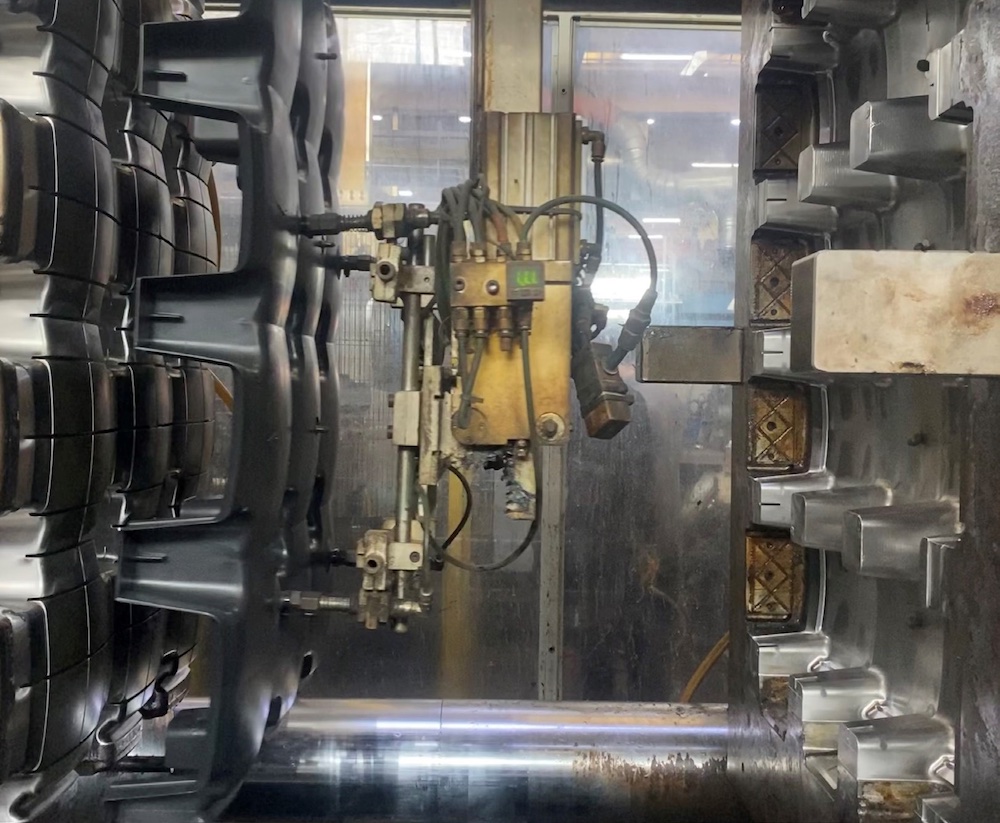
D. Quali sono gli aspetti tecnici dei quali un progettista deve tenere conto?
R. Uno degli aspetti fondamentali è la sostenibilità. Viviamo su un pianeta che deve essere rispettato quindi l’attenzione a non sprecare risorse e minimizzare l’impatto ambientale è fondamentale. In secondo luogo, dare valore alle strutture esistenti, più che al nuovo.
D. Qual è la situazione del mercato attuale e quali sono le previsioni per il 2023?
R. Il 2022 è stato un anno molto positivo. Abbiamo realizzato molti investimenti nell’ultimo triennio e il nostro fatturato è sicuramente in crescita. A livello di mercato si percepisce un po’ di incertezza, ma attualmente non notiamo grosse oscillazioni rispetto al 2022. Contiamo di chiudere l’anno in positivo, mantenendoci sugli stessi standard dello scorso anno.